Machining
Machining is an extraordinary manufacturing process where machinists and machine operators transform workpieces by removing material using cutting tools and machines. Operations such as turning, milling, drilling, and grinding create the required shapes and sizes. However, machining also includes machine tool accessories, measuring and inspection equipment, oils and additives, workholding devices, coolants, and cutting fluids to make things run smoothly.
Machining BY CATEGORY
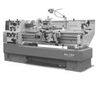
Machinery
Mechanical devices that perform tasks, automate processes, and drive productivity across various industries.
Show Machinery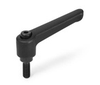
Machine Tool Accessories
Components that optimize performance, increase versatility and improve precision in machining operations.
Show Machine Tool Accessories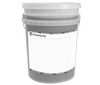
Cutting Oils & Additives
Enhance cutting performance, extend tool life, and improve machining results.
Show Cutting Oils & Additives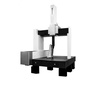
CMM Machine Components
Essential components and software that enable precise and accurate measurements.
Show CMM Machine Components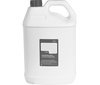
Coolant & Cutting Fluids
Optimize machining, dissipate heat, and improve tool life.
Show Coolant & Cutting Fluids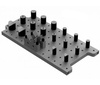
Measuring and Inspection
Essential for accuracy, quality, and compliance in industries.
Show Measuring and InspectionMachining POPULAR PRODUCTS
JET 723520K JWDS-1632 Drum Sander 1.5HP 1PH 115V Open Stand
Brand JET Tools
Model 723520K
JET 414559 HVBS-712 7" x 12" Horizontal / Vertical Bandsaw
Brand JET Tools
Model 414559
JET 350017 JMD-15 Mill/Drill With R-8 Taper 115/230V 1Ph
Brand JET Tools
Model 350017
JET 321378 BDB-919 Belt Drive Bench Lathe 3/4HP 115V Single Phase
Brand JET Tools
Model 321378
Powermatic 1791303 WP2510 25" Planer 15HP 3PH 230/460V
Brand Powermatic
Model 1791303
Powermatic 1791293 OES9138 Oscillating Edge Sander 3HP 3PH 230/460V
Brand Powermatic
Model 1791293
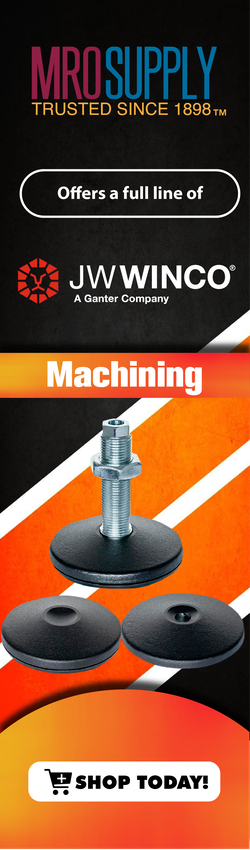
About Machining
In the manufacturing sector, machining stands as a cornerstone, a proud monument to truth, justice, and other legendary cliches. It involves using machinery, cutting tools, and coolants to shape, cut, or modify material—often metal—to create specific parts or structures. From the smallest screws in your eyeglasses to the massive components of an aircraft, machining plays an integral role. And after work, those screws and components get together and have a beer because, hey, it’s machining Miller time!
In metal and woodworking, various machinery plays crucial roles in shaping raw materials into desired forms. What kind of machinery? Glad you asked. Metalworking machinery such as lathes, milling machines, planers, bandsaws, and sanders are employed to turn, cut, drill, or saw metals with high precision. But, wait—there’s more! Because woodworking machinery, such as table saws, planers, and sanders, are used for cutting, smoothing, and joining wood pieces, occasionally, if they’re lucky, in the bonds of holy matrimony.
Coolants and cutting fluids are integral to machining, offering several key benefits. We will now list these benefits in no particular order so as not to upset or offend those coolants and cutting fluids. First, they reduce the heat generated during machining, preventing damage to both the tool and the workpiece. This heat reduction also helps maintain the dimensional accuracy of the workpiece, as excessive heat can cause materials to expand or warp. Which brings up a “Star Trek” question: Can a warp engine warp? And would Scotty know how to fix it? In addition, coolants and cutting fluids reduce friction between the cutting tool and the workpiece, allowing for smoother operation and prolonging tool life. These fluids also assist in removing chips or swarf from the cutting area, keeping the workspace clean and ensuring a high-quality finish. Now, getting back to “Star Trek”, is “Swarf” a long-lost relative of Worf?
Workholding devices are crucial in securing materials or workpieces for machining. Chucks, faceplates, and collets are among the various devices for lathes, while vises and fixtures work well on milling machines and drill presses. And wouldn’t that be a great name for a buddy cop movie: Mill ‘n’ Drill? One’s from The Netherlands, the other’s a part-time plumber! Each device has its specific uses and advantages, and selecting an appropriate one can significantly impact the efficiency and precision of machining tasks. But be warned: selecting an inappropriate one could cause rips in the space-time continuum along with headaches and upset tummies.
It's impossible to overstate the importance of measuring and inspection in machining. (If you like, you can try overstating. We’ll wait.) Accurate measurements ensure that machined parts meet specified tolerances and fit together correctly in assemblies. This process not only safeguards the quality and functionality of the final product but also minimizes waste by detecting errors early in the production cycle. For those who prefer maximizing waste, we don’t know what to say. Typical measuring and inspection tools include micrometers, calipers, dial indicators, and coordinate measuring machines. Atypical measuring and inspecting tools include licorice whips, snails, hockey pucks, and penny loafers.
Machining is an essential process in manufacturing, transforming raw materials into precise components, parts, and products. Which sounds like a “Schoolhouse Rock” song: “Machining lives in all our hearts/Transforming components, products, parts.” Combining excellent machinery, work-holding devices, coolants, and inspection equipment provides efficiency, precision, and reliability in each machining operation.